Anodising FAQ
52 Years of Manufacturing Excellence
History of anodised aluminium
Anodising is a very old and established process and was developed for commercial applications in the early 1930’s. It is still in service on buildings built in the 1950’s, Anodising continues to stand the test of time today.
What is anodising?
Is the process for producing a translucent film of aluminium oxide which forms an integral part of aluminium. This is produced by applying direct current through a suitable electrolyte (dilute sulphuric acid) in which the aluminium is the anode and a suitable material e.g. (lead) is the cathode.
How long does the anodising process take?
It physically only takes a few hours to process and pack a part. We need anywhere from a few days to a few weeks to plan and process projects. General Lead times of 1 – 2 weeks apply and lead times of longer than four weeks for anodising are rare.
What is the biggest piece that can be anodised?
Sapphire can anodise extrusions, sheets and fabricated or folded components within the following dimensions.
- Length = up to 6.5 metres
- Depth = up to 1.3 metres
- Width = up to 550mm
What can be polished?
Polishing is a separate process which is performed prior to chemical (polishing) brightening. This is done by mechanically polishing the aluminium by a buffing process. This removes minor to medium ( scratches, die lines and marks) that are often present on aluminium, however it cannot not remove deep scratches, die lines and roadburn which will remain visible after the anodising process.
Sapphire can polish extrusion upto a maximum width and height of 200mm and to a maximum length of 6500mm.
What can be brushed/linished?
Brushing/Linishing is also a separate process which is performed prior to chemical (polishing) brightening or matt processes by passing the aluminium under an abrasive belt to give a coarse uniformed linished appearance as is generally seen on picture frame extrusions.
Please Note: Ultra/Fine/Brushing/ Linishing can only be performed on flat surfaces up to 150mm in width for extrusions or up to 1200mm for sheet. Linishing finish is not recommended for Shopfront, partitioning, furniture or any item where it can come into physical contact as it can produce sharp edges that can cause physical damage such as cuts or laceration.
What can be anodised?
Sapphire’s process for anodising only lends itself to aluminium extrusion, sheet and plate of certain alloys. As mentioned above anodising is a reaction with the alloy surface you wish to coat and the resulting coating will depend on the quality and purity of the alloy used. The following international alloys are recommended by Sapphire for consistent anodising results (all alloys should be Prime Billet, no remelt).
Extrusion
- 6060T5
6063T5
6463T5 (Used for high quality bright finishes)
Sheet
- 5005 H14 – 34
5205 H14 – 34
Sheet alloys and quality vary from each supplier and defects often can only be identified after anodising is completed. It is reccommeded that if you have a large project to anodise, that you obtain a sample of the sheet you intend to use and send to us to test prioir to manufacture. Ensure all product is manufactured from the one batch of sheet to minimise defects and colour variation.
Defects in Sheet Alloy that can affect Colour and finish uniformity
1) Colour variation
5005 Alloy has a wide tolerance in the level of magnesium Mg present in the alloy and this can lead to wide colour variation if different batches are used, When there is a high amount present it will leave the anodised coating as a dark grey which will then affect colouring consistency
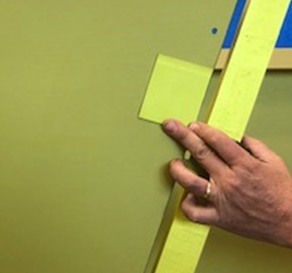
2) Zebra/Tiger Striping
This is a defect that can appear in sheet during the anodising process that will highlight inconsistent alloy that occurs during the sheet manufacturing process.
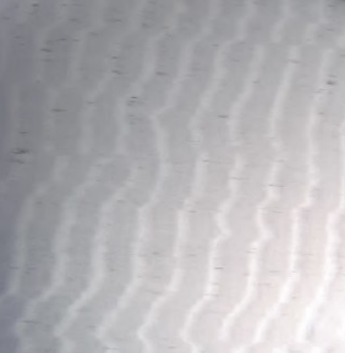
3) Banding / GT Stripes
This is a defect that can appear in sheet during the anodising process that will highlight inconsistent alloy that occurs during the sheet manufacturing process.
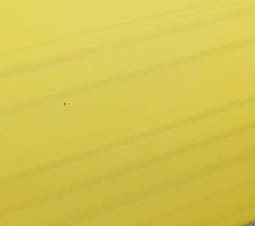
Folding & Bending
When a folded panel is required to be anodised this should be folded to the thickness required ie 3mm, DO NOT V CUT FOLD this will break during the anodising process and the panel will disintegrate.
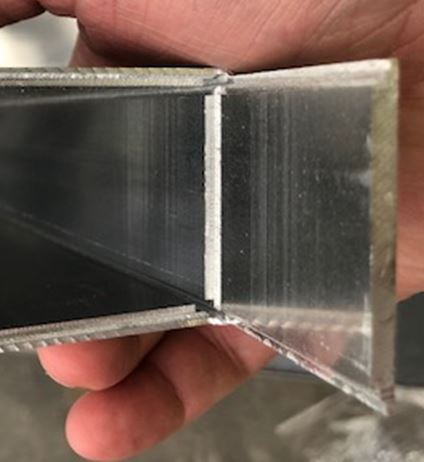
Welding and Anodising
When parts require welding prior to anodising, care should be taken in the selection of the correct Filler Rod or wire used for the process. If a colour match is required on the part and the weld then 5356 Rod is to be used to ensure as close a match as possible. Differences can still occur from heating of the part in the welding process that can change the alloy of the part. If bulk quantities of parts are required to be manufactured then a prototype should be produced and tested for colour matching suitability prior to bulk manufacture.
How thick is the coating?
Anodising is a very thin coating of immense hardness measured in microns.
Internal uses are generally between 10um – 20um. (Dependant on Colour Shade)
Exterior uses are between 15um – 25um (refer to guide on selection of Anodised Coatings)
A micron (um) is 1/1000 of a millimetre for example a cigarette paper is 7um.

How hard is anodising?
Anodising is aluminium oxide which is the second hardest substance known to man, only a diamond surpasses anodising in hardness. Anodising can increase the hardness of the untreated aluminium surface by more than 3 times.
How long will anodising last?
Anodising properly specified and maintained will virtually last indefinitely. A normal service life in excess of fifty years for Sapphire AA25 coatings can be expected (subject to proper and regular maintenance), making the coating ideal for commercial and monumental use.
What are Racking or Jig Marks?
In order to anodise aluminium we need to hold on to the material in such a way as to pass an electrical current through it, this is commonly known as a jig mark. All items for anodising need to allow for a jig mark which is generally removed by the customer after anodising. You should allow the following for jig marks.
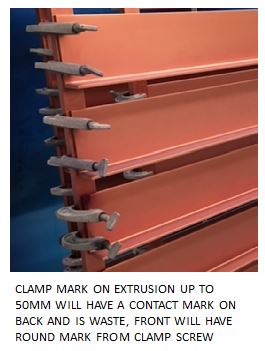
Extrusion = up to 50mm from each end
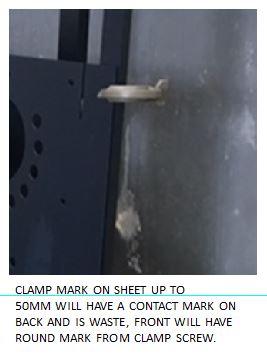


How do you colour the anodising?
1. Absorption
The anodised aluminium is immersed in a tank full of dye and the dye absorbs into the pores of anodised coating until the desired shade is obtained.
2. Two Step
3. Spectral®
Spectral is a three step process which manipulates the anodised coating to create different light refraction prior to 2 step colouring. This process creates a whole new palatte of colours that perform well against UV. (Refer to Spectral Tab for more information)
Colour inspection
As with timber, brick and other traditional building materials, no two pieces of anodised metal look exactly alike. Slight colour variations are due to differences in alloy composition; the grain size and grain orientation developed during the heat treatment or cold working processes; and variations in the parameters of the colour anodising processes.
The designer can reduce the apparent effect of colour variation by breaking up expanses of colour with other colours, changes of plane or other architectural treatments.
When inspecting Anodised finishes for colour and finish tonality certain factors must be taken into consideration.
1. Light conditions
As the Anodised finish is translucent whether it is matt or bright finished it will tend to reflect light like gemstones, It this property that gives life to finish giving it a different appearance depending on the angle and intensity of the light source it is inspected in.
2. Distance from product viewed
3. Differences in perception of colour
Is anodising safe?
Anodising is a safe process that is not harmful to human health. An anodised finish is nontoxic and chemically stable and therefore does not have an MSDS. It will not decompose and increases the fire protection from 600 degrees Celsius to around 2000 degrees Celsius.
For additional information refer to one of the following standards that applies to your region
- AS1231-2000 – Australia
- AAMA 611-98 – American Architectural Manufacturers Association
- ASTM B580-79(2000) – ASTM International
- BS EN 12373-2001 – British & European Standards
- ISO7599-1983 – International Standard